Pesce Quality Process Control and Automation Solutions for Food Manufacturing Plants
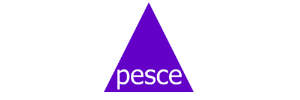
Pesce provides effective and cost-efficient process control and automation solutions, customised to meet a client’s food manufacturing requirements.
Pesce’s engineers are involved with the entire project workflow of an automation system from conceptual design through to commissioning and product verification.
The company specialises in highly integrated solutions that can easily be scaled to suit a wide range of applications. Pesce has built systems that also incorporate multiple programmable logic controllers (PLC), remote terminal units (RTU), and other sophisticated devices.
Modern process control and automation systems in accordance with food industry requirements
Pesce provides a variety of flexible services for the implementation and maintenance of its process control and automation systems. Helping transition old infrastructure to more modern configurations, the company provides production recording and reporting for standards compliance, as well as for overall equipment effectiveness (OEE).
For its automation systems, Pesce makes modifications to support many large and small process changes. The company also integrates a range of disparate systems into a single supervisory control and data acquisition (SCADA) application, with redundancy and multiple work stations.
Pesce makes long-term commitments in providing its products, services, and advice. The company still regularly undertakes projects with its very first client.
High-performance automation systems for quick response times and secure data
Automation system performance has several aspects. Pesce’s team of well-trained and dedicated engineers help ensure that the performance of its projects exceed client expectations. The company considers usability, interoperability, response times, data integrity, and security when designing a system.
Pesce’s automation systems are noted for their smart design, fast and reliable networks, efficient operator interfaces, effective technologies, and comprehensive documentation. Each solution is thoroughly tested and supported with a responsive service and after-sales support.
Data collation and integration for food production control systems
Pesce has designed, built, and commissioned control systems for applications requiring accurate and reliable data. The company integrates production and process monitoring solutions to automatically send collated data to business systems. This provides critical plant monitoring abilities and informed maintenance requirement estimates. In addition, the system operator can manually enter information into the product data stream, or it can be issued to a database when required.
Providing complete business intelligence allows vertically integrated data to flow both ways, helping to control production parameters and performance.
Food manufacturing plant operator interface systems for control of data and production
Pesce builds intuitive manufacturing plant operator interface suites designed for easy modification for use with data and work flows. Whether a simple interface panel or large integrated human machine interface (HMI) or SCADA system is required, Pesce ensures a customised solution using more than 30 years of development experience.
As plant operators can spend many hours a day using computers, Pesce has designed its operator interface suite using techniques to minimise eye fatigue and reduce critical errors in operator actions.
While many of Pesce’s customised solutions are based in Schneider Electric’s Citect suite, the company has a wealth of experience in other HMI and SCADA systems and aims to always offer the best suited system to its clients’ applications.
Customised software for plant primary control equipment used in food processing
Including PLC methods such as ladder, function block, sequential function charts (SFC), and statement list methods, Pesce has vast programming experience to provide solutions, which ensure fundamental control equipment is correctly configured for smooth SCADA and operator interface implementation. With timely reactions for both day-to-day and emergence events, the software is reliable and designed with performance in mind.
Pesce’s specialised knowledge, testing regimes, and documentation standards enable the company to deliver very high quality solutions that are proven fit for purpose.
High-performance food process control systems with secure communication
Pesce helps assess the quality of pre-existing or partially completed process control systems, as well as providing new solutions. Each offering provides high performance based on robust technology. System designs are easily implemented, with documented functionality, helping manufacturing plants to meet industry requirements.
Alongside recommendations for overall system improvements, Pesce can advise the most suitable communication architectures. The company designs solutions with ample bandwidth for expansion, with experience in serial (RS232 / 422 / 485), proprietary (Tiway, Profibus, ControlNet, DeviceNet, and many remote input/output (I/O) networks), as well as copper and fibre-optic industrial ethernet communications.
Products and Services
Video
White Papers
Press Release
This project was the result of a discussion with the staff of a dairy processing factory about updating motor equipment, specifically upgrading from simple hardwired input/output (I/O) motor monitoring to include more diagnostic information.
Read morePesce was involved in a project that was the result of very detailed tender specifications for a system to monitor and manage electrical use throughout a large campus.
Read moreRegional Offices
Unit 4, 106 Mawson Place,
Mawson ACT 2607
Australia